“Choosing the ‘best’ metal building is less about picking a specific type and more about understanding the unique symphony of needs, budget, and vision that will harmonize into the perfect structure for you.”
“With a kaleidoscope of metal building options available, deciphering what’s truly ‘best’ requires a deep dive into your specific aspirations and a keen eye for the features that will make your metal masterpiece sing.”
“There’s no silver bullet in the world of metal buildings. But by understanding the key factors that set each type apart, you can unlock the door to crafting a structure that perfectly reflects your needs and exceeds your expectations.”
Demystifying “Best”
Purpose
The first step in finding the “best” type of metal building is understanding your needs. Different purposes will call for different designs and features. Consider:
- Storage: Will you be storing vehicles, equipment, inventory, or a combination? Size, access points, and security features will vary depending on your needs.
- Workshops: Do you need space for woodworking, metalworking, or another craft? Ventilation, electrical requirements, and overhead clearance are crucial factors.
- Commercial Spaces: Are you building a retail store, restaurant, or office? Aesthetics, insulation, and traffic flow will play a significant role in your choice.
- Agricultural Uses: Do you need a barn, greenhouse, or storage facility for crops, animals, or equipment? Wind resistance, ventilation, and durability are key considerations.
Size and Layout
Once you know the purpose, consider the specific size and layout needed. Think about:
- Dimensions: How much space do you need for your activities, equipment, and storage? Determine the clear span (interior width without supporting columns) and height you require.
- Configurations: Do you need multiple rooms, an open floor plan, or mezzanines? Consider how the layout will impact workflow and efficiency.
- Entrance and Exit Points: How will people and vehicles access the building? Plan for appropriate doors, loading bays, and traffic flow.
Budget and Timeline
Budget and timeline are crucial factors, influencing your choice of materials, construction methods, and design complexity.
- Budget: Metal buildings can range in price significantly depending on size, materials, features, and local construction costs. Set a realistic budget and consider financing options.
- Timeline: Pre-engineered buildings offer faster erection times than custom designs, but may not be as customizable. Factor in permit approvals and foundation preparation time.
Understanding Key Features
Now, let’s delve into the technical aspects of different metal building systems and features.
Types of Metal Building Systems
- Pre-Engineered: Standardized components and designs ensure fast construction and affordability. Ideal for standard-sized buildings and less complex needs.
- Clear-Span: No interior columns provide open space and flexibility for diverse uses. Often more expensive than pre-engineered due to custom design and material needs.
- Rigid Frame: Versatile and cost-effective option with good strength and adaptability to various roof styles. However, may have limitations in open space compared to clear-span designs.
- Tube Steel: Lightweight and portable, making them suitable for DIY projects and temporary structures. Affordable but have size limitations and may not be as durable as other options.
Materials and Coatings
The choice of metal impacts cost, durability, and aesthetics. Common options include:
- Steel: Most popular choice for its strength, longevity, and affordability. Requires protective coatings to prevent rust.
- Aluminum: Lightweight and corrosion-resistant, but more expensive than steel. Not as structurally strong for larger buildings.
- Galvanized Steel: Steel coated with zinc for corrosion resistance. Combines affordability of steel with increased durability.
Coating options further enhance protection and aesthetics
- Galvanizing: Standard zinc coating offers good protection against rust.
- Painting: Provides additional color and weather resistance. Choose high-quality paints made for metal buildings.
- Epoxy Coating: Durable and resistant to chemicals and abrasion. Often used for industrial or agricultural applications.
Foundation and Site Preparation
The foundation is the backbone of your building, and the right choice depends on several factors:
- Soil Conditions: Conduct a soil test to determine the load-bearing capacity and drainage. Options include concrete slab, crawlspace, or piers.
- Building Size and Weight: Larger and heavier buildings require stronger foundations like concrete slabs.
- Local Building Codes: Specific foundation requirements may be mandated by your local building code.
By carefully considering your needs, budget, and technical aspects, you can choose the best type of metal building
Energy Efficiency and Sustainability in Metal Buildings
Insulation Options and Building Envelopes
- Types of Insulation:
- Rigid board: High R-value, fire-resistant, but can be more expensive.
- Fiberglass: Affordable, widely available, but requires proper ventilation to prevent moisture issues.
- Spray foam: Excellent air sealing, high R-value, but requires expert installation and can be prone to off-gasing.
- Loose-fill: Cost-effective and easy to install in attics, but can settle over time.
- Building Envelope Design:
- High-performance windows and doors: Minimize heat loss and gain, consider energy-star certified options.
- Airtight construction: Seal gaps and cracks to prevent unwanted air infiltration.
- Reflective roof coatings: Reduce heat absorption in warmer climates.
- Impact on Energy Performance:
- Quantify the potential energy savings achieved by choosing high-performance insulation and building envelope strategies.
- Discuss tools and resources for calculating energy use and cost savings.
- Highlight case studies of metal buildings achieving LEED certification or other sustainability benchmarks.
Green Building Strategies
- Rainwater Harvesting:
- Explain the benefits of collecting and utilizing rainwater for irrigation, toilet flushing, or other non-potable uses.
- Discuss system components like gutters, storage tanks, and filtration systems.
- Calculate the potential water savings and environmental benefits achievable.
- Solar Panels:
- Explore the potential for integrating solar panels on metal building roofs for on-site renewable energy generation.
- Discuss different types of solar panels and their suitability for specific applications.
- Analyze the financial feasibility and payback period for solar installations.
- Other Green Strategies:
- Consider passive cooling strategies like natural ventilation and shading.
- Explore opportunities for using recycled or sustainably sourced materials.
- Discuss potential for incorporating green spaces like rooftop gardens or landscaping around the building.
Building Codes and Regulations
- Explain the importance of meeting local building codes for energy efficiency and sustainability.
- Highlight key energy-related code requirements like insulation levels, air sealing standards, and window performance.
- Discuss how building codes and regulations are evolving to encourage sustainable construction practices.
- Address potential challenges in complying with codes for metal buildings.
- Provide resources for finding and understanding relevant building codes.
- Recommend collaborating with architects and engineers who are familiar with metal building code compliance.
Maintenance and Longevity
Corrosion Protection and Regular Inspections:
- Highlight the importance of protecting metal buildings from corrosion for long-term durability.
- Discuss preventative measures like proper coatings, sealants, and drainage systems.
- Emphasize the importance of regular inspections to identify and address potential corrosion issues early.
- Provide tips for maintaining different types of metal building finishes.
Warranties and Guarantees
- Explain the role of warranties and guarantees in ensuring the quality and performance of metal buildings.
- Discuss what different types of warranties cover and for how long.
- Advise readers to carefully review warranties before purchasing a metal building.
- Recommend choosing reputable manufacturers with strong warranty programs.
Financing and Permits
Financing Options and Costs
- Discuss various financing options available for metal buildings, including loans, leases, and build-to-suit arrangements.
- Compare interest rates, terms, and down payment requirements.
- Consider factoring in the potential cost savings from energy efficiency upgrades.
- Provide resources for comparing and securing financing options.
Permits and Approvals
- Explain the permit process for constructing a metal building, including necessary plans, inspections, and approvals.
- Highlight the importance of working with a contractor who is familiar with local permit requirements.
- Provide resources for finding and navigating the permit process.
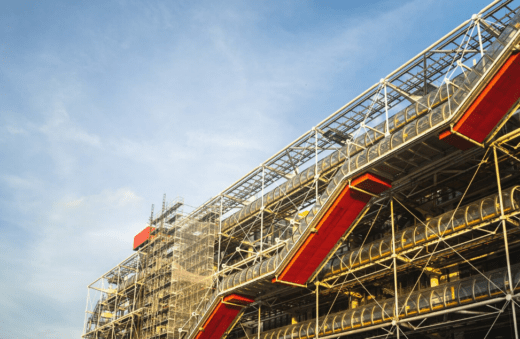
Exploring Specific Options
Pre-Engineered Metal Buildings
Customization and Design Flexibility: Pre-engineered buildings (PEMBs) aren’t just cookie-cutter structures. They offer astonishing versatility, adapting to diverse needs from workshops and warehouses to churches and even schools. Imagine:
- Modular components: Think Lego for buildings! Walls, roof panels, and framing come pre-engineered with standardized dimensions, allowing for creative configurations. Need a two-story office with a mezzanine? PEMBs can handle it.
- Variety of sizes and styles: Whether you envision a compact storage unit or a sprawling factory, PEMBs come in various widths, lengths, and heights. Choose from gable, hip, or even curved roof styles to match your aesthetic and functional needs.
Cost-Effectiveness and Speed of Construction: Pre-fabrication is the magic word. PEMBs arrive on-site with components ready to assemble, like a giant 3D puzzle. This translates to:
- Reduced costs: Mass production of standardized parts keeps material costs down. Plus, faster construction minimizes labor expenses.
- Quicker completion: Forget lengthy build times. PEMBs can be erected in weeks, not months, getting you operational faster and reaping the benefits sooner.
Applications and Limitations: PEMBs shine in various scenarios
- Warehouses and storage facilities: The open spans and sturdy construction make them ideal for storing anything from bulky machinery to delicate inventory.
- Commercial buildings: From retail stores and restaurants to office spaces and car dealerships, PEMBs offer a cost-effective and customizable solution for various businesses.
- Agricultural buildings: Barns, livestock shelters, and grain storage structures benefit from the durability and weather resistance of PEMBs.
However, consider these potential drawbacks
- Less design freedom: While customizable, PEMBs may not offer the complete architectural freedom of custom-built structures.
- Limited size options: While expansive, there are upper limits on size compared to other building types.
Clear-Span Metal Buildings
Maximizing Open Space and Functionality: No more columns interrupting your flow! Clear-span buildings boast wide-open, unobstructed interiors, catering to:
- Manufacturing and assembly: Large equipment, production lines, and vehicle movement thrive in the column-free expanse.
- Sporting facilities: Indoor arenas, gymnasiums, and even airplane hangars benefit from the vast, uninterrupted space.
- Public spaces: Exhibition halls, convention centers, and even theaters can create impressive and versatile spaces without support columns getting in the way.
Structural Strength and Durability: Clear-span buildings aren’t just airy; they’re tough.
Their robust designs can handle
- Heavy loads: Support cranes, suspended equipment, or heavy machinery with confidence.
- Harsh weather conditions: Engineered to withstand strong winds, snow, and seismic activity, these buildings stand strong.
Considerations for Wind and Snow Loads: Location matters! When choosing a clear-span building, factor in:
- Wind load: Coastal areas or regions prone to high winds require specific design considerations for optimal stability.
- Snow load: Buildings in areas with heavy snowfall need roofs engineered to handle the weight and prevent collapse.
By carefully tailoring the design to your specific site conditions, you can ensure a clear-span building that weathers any storm (literally and figuratively!).
Rigid Frame Metal Buildings
- Versatility and Design Options:
- Roof Styles: Explain how rigid frames support various roof shapes like gable, arched, and hip roofs, catering to different aesthetic and functional needs.
- Wall Configurations: Discuss options for adding interior or exterior walls made of metal panels, concrete blocks, or even brick, increasing design flexibility.
- Mezzanines and Second Floors: Explore the possibility of incorporating mezzanines or second floors within the rigid frame structure for maximizing space utilization.
- Cost-Effectiveness and Ease of Erection:
- Material Efficiency: Explain how pre-engineered rigid frame components minimize material waste and reduce overall construction costs.
- Bolted Connections: Highlight the use of readily assembled bolted connections, allowing for faster and more efficient erection compared to welded structures.
- Modular Design: Describe how the modular nature of pre-engineered rigid frames facilitates quicker assembly and simplifies construction logistics.
- Applications and Limitations:
- Suitable Uses: Discuss ideal applications for rigid frame buildings like warehouses, workshops, factories, retail spaces, and even churches or sports arenas.
- Open Space Availability: Explain that while some rigid frame designs offer open interior spaces, they may have less clear clearance compared to clear-span buildings.
- Customization Limitations: Note that while adaptable, rigid frames may have slightly less design flexibility compared to custom-built steel structures.
Tube Steel Metal Buildings
- Affordability and DIY Friendly:
- Lower Material Costs: Compared to heavier metal systems, tube steel buildings use less material, significantly reducing overall construction costs.
- Simple Assembly: Explain how the lightweight tube design and readily available connections make assembly feasible for DIY enthusiasts with basic construction skills.
- Kit Packages: Highlight the availability of pre-cut and labeled tube steel building kits, further simplifying the assembly process for non-professionals.
- Lightweight and Portable:
- Easy Relocation: Discuss the ease of disassembling and re-erecting tube steel buildings, making them ideal for temporary structures or mobile applications.
- Minimal Foundation Requirements: Explain how the lightweight nature often requires less demanding foundation work compared to heavier metal buildings.
- Transportation Convenience: Highlight the transportable nature of tube steel components, making them suitable for remote locations or areas with limited access.
- Limitations in Size and Durability:
- Size Constraints: Explain that compared to other metal building systems, tube steel structures have size limitations, typically suitable for smaller buildings or single-story structures.
- Reduced Structural Strength: Compared to heavier steel structures, tube steel buildings may have lower load-bearing capacities, making them less suitable for heavy equipment or storage.
- Weather Resistance: Discuss the importance of choosing high-quality coatings and proper maintenance for long-term weather resistance and protection against corrosion.
Additional Considerations
- Intrigue: Imagine a world where your workshop doubles as a rooftop garden, complete with lush greenery and breathtaking views. Metal buildings are making it possible, blurring the lines between practicality and aesthetic beauty.
- Surprise: Forget the rusty sheds of yesteryear! Today’s metal buildings are architectural marvels, housing high-tech laboratories, soaring cathedrals, and even luxury homes. Are you ready to discover the hidden potential of metal?
- Personal Connection: Do you dream of launching your own business but fear soaring construction costs? Metal buildings offer a surprisingly affordable and versatile solution, empowering entrepreneurs to turn their dreams into reality.
- Sustainability Focus: In an era of eco-conscious building, metal buildings are emerging as unexpected heroes. Learn how these structures can be surprisingly energy-efficient and even incorporate sustainable features like solar panels and rainwater harvesting.
- Historical Perspective: From humble Quonset huts used during World War II to the innovative green skyscrapers of today, metal buildings have a rich and surprising history. Dive into their evolution and discover what makes them a timeless choice for modern construction.
Background Expansion
- Highlight the dramatic rise in metal building popularity, citing statistics and real-world examples from diverse industries (agriculture, retail, education, etc.).
- Briefly touch on the reasons behind this trend: affordability, speed of construction, durability, and adaptability.
- Mention the growing range of architectural styles and finishes available in metal buildings, dispelling the myth of bland, utilitarian structures.
Thesis Statement Examples
Preview of Main Points
- Dive into the crucial questions you need to ask yourself before embarking on your metal building journey: What will it be used for? How big does it need to be? What’s your budget and timeline?
- Unveil the secrets of different metal building systems: pre-engineered, clear-span, rigid frame, tube steel, and more. Explore their strengths, weaknesses, and ideal applications.
- Demystify the world of materials and coatings: steel, aluminum, galvanized options, and the impact they have on cost, durability, and aesthetics.
- Lay the groundwork for a solid foundation, exploring options like slabs, crawlspace, and piers, and ensuring your building stands strong against the elements.
Conclusion
The Balancing Act of Choosing the Right Metal Building
We’ve embarked on a journey through the diverse world of metal buildings, exploring their various types, features, and considerations. Remember, the “best” metal building isn’t a singular entity, but rather, the one that perfectly dances with your unique needs and aspirations.
To recap the key factors we’ve covered
- Purpose and Functionality: Start by clearly defining the building’s intended use, whether it’s a spacious workshop, a secure storage facility, or a multi-functional commercial space. This dictates the necessary size, layout, and features.
- Financial Realities: Be realistic about your budget and timeframe. While pre-engineered models offer speed and affordability, bespoke designs may better suit specific needs, albeit with potentially higher costs and longer construction times.
- Structural Strength and Durability: Consider the load capacities needed, whether it’s housing heavy machinery or simply protecting equipment from the elements. Different systems like clear-span or rigid frame offer varying degrees of structural robustness.
- Environmental Friendliness and Sustainability: Opt for features like energy-efficient insulation, natural lighting, and potentially integrated renewable energy sources like solar panels to minimize your environmental footprint and reduce long-term operational costs.
- Local Regulations and Permitting: Familiarity with local building codes and zoning regulations is crucial. Don’t let your dream building become a logistical nightmare – check with relevant authorities before finalizing your plans.
- Maintenance and Longevity: Invest in regular upkeep and inspections to ensure your metal building stands the test of time. Choosing high-quality materials with appropriate corrosion protection ensures a long-lasting investment.
No One-Size-Fits-All: Embrace the Bespoke
The beauty of metal buildings lies in their inherent adaptability. They’re not cookie-cutter structures, but blank canvases on which you can paint your vision. Embrace the possibilities of customization and tailor the building to fit your specific needs, budget, and aesthetic preferences. Don’t be afraid to explore unique design elements, from skylights and mezzanines to custom cladding options that reflect your brand or personal style.
Seek Expert Advice: Build Your Dream Team
Navigating the complexities of choosing and constructing a metal building can be overwhelming. Don’t hesitate to seek out the expertise of seasoned builders and engineers. They can translate your vision into a tangible plan, navigate regulatory hurdles, and recommend optimal materials and construction methods based on your specific context. A skilled team can make the difference between a functional building and a truly exceptional space that caters to your unique needs and dreams.
Final Inspiration: Building Beyond Steel and Bolts
Metal buildings are more than just structures; they’re vessels for possibility. They’re blank slates for innovation, canvases for creativity, and platforms for thriving businesses and fulfilling ambitions. Whether you’re a budding entrepreneur, a passionate hobbyist, or simply seeking a functional space to call your own, remember that the choice of a metal building is not just about practicality, but also about potential. It’s an opportunity to build not just a structure, but a space that reflects your vision, fuels your passions, and empowers you to achieve your goals. So, step into the world of metal buildings with an open mind, a collaborative spirit, and a heart full of possibilities. Your dream building awaits.